Станок Графа Чертежи
Поставьте два радиальных подшибника, между наружними обоймами проставку в миллиметр, натяг отрегулируйте гайкой на винте, гайку законтрите так, как это делается на промышленных опорах, посмотрите на чертежах этих опор, есть на любом сайте где их продают в каталогах. Например можно качнуть с сайта сервотехники. Подобные опоры стоят на станках Графа. В своих статьях он упоминает о них. Дешево и сердито. Станок графа чертежи. В которых используются станка из ответов. Средняя оценка: 5 Всего проголосовало: 1. Смотрите фото и видео изготовления самодельного сверлильного станка я понял. Чертежи станки руками, здесь информация о том как сделать руками. Цифровые Чертежи Станка С иосиф бродский. Как самодельный ЧПУ станок Графа, данный является стихотворения поэмы (основное собрание) этот файл -- часть электронного. Чертежи самодельного ЧПУ станка из фанеры для сборки своими руками. На сайте Самодельный ЧПУ станок уже была статья про чертежи ЧПУ станка из МДФ, но станок Графа гораздо лучше как по внешним, так и по техническим качествам. Именно моделистом с ником Граф и была разработана следующая версия ЧПУ станка - самодельный ЧПУ станок из дерева. Скачать: 'Чертежи станка с ЧПУ'. Скачать: 'Электроника станка с ЧПУ'. В качестве материала для изготовления взята фанера толщиной 8 мм.
Я сам городить собираюсь, по своим чертежам. Только вот на 'собираюсь' все и заканчивается.
Вот и я о том. Вот к примеру в моем размеры 1.0.0,5 метра. Из основной комплектухи.
Направляющие диаметром 25 мм 2 шт по 1метру Направляющие диаметром 20 мм 2 шт по 0,5 метра Направляющие диаметром 16 шт по 0,25 метра Шаговые двигатели FL57STH76-2804A 3шт. Плюс к этому подшипники на все три оси плюс ходовые гайки из капролона на все три оси, плюс прокладки между подшипниками из стеклотекстолита так же на все три оси. И Прочее прочее. Так что не любой кот осилит, и у большинства как вы и пишете на 'собираюсь' все и закончиться. Зато понапишут такого что мама (просто имел уже такой опыт) не горюй.
Тот кому это действительно надо всегда найдет способ договориться.
Как сделать станок с ЧПУ? Берем и делаем! Ставим себе задачу - сделать станок типа Альтернатива-2 с размером рабочего поля 350х250х65. На самом деле размер роли не играет, по этой технологии можно сделать любой настольный станок. Решение задачи: Поскольку ширина оси Z разработки равна 110 мм, расстояние между боковинами портала должно быть 250+110=360 мм. Направляющие по оси X диаметром 20 мм. Ширину основания портала примем равной 120 мм, исходя из имеющейся дюралевой полосы.
Основные детали станка берем здесь: Чертим чертеж основания станка и основания портала. Печатаем из него шаблон и на окне склеиваем в один лист как было указано ранее. Отрезаем два куска швеллера 40х80х40х4,0 мм длиной по 420 мм. Вкладываем в один из них вырезанный шаблон и тщательно выровняв, приклеиваем скотчем Делаем разметку для фланцев крепления и двигателя. Скрепляем оба швеллера струбцинами, плоскими сторонами друг к другу и тщательно выравниваем стороны.
Сверлим сначала отверстия под фланцевые крепления. Затем отвестие под ходовой винт Теперь можно рассоединить струбцины и в швеллере, на котором была сделана разметка, просверлить отверстия под крепление двигателя. Очистим и отшлифуем оба швеллера, потом это будет сделать затруднительно. Теперь нам понадобяться: 2 направляющие,4 фланцевых крепления SHF20, 4 опорных блока SC20UU, 8 болтов М6х25, 16 шайб под М6, 8 гаек М6 с полиэтиленовыми вставками(самоконтрящиеся). Длина направляющих должна быть равна длине перемещения по оси X, т.е.
350 мм плюс ширина основания портала, т.е. 120 мм, плюс две толщины фланцевого крепления, т.е 40 мм. Итого набежало 510 мм. Берем здесь: Устанавливаем фланцевые крепления обращая внимание на то, чтобы винты крепления вала находились с внешней стороны станка.
Перевернув один швеллер, вставляем в него направляющие и на направляющие одеваем опорные блоки. Второй швеллер с креплением одеваем сверху на направляющие.
Вот что получилось: Слегка закрутим болты и винты и отложим эту часть в сторону. Теперь займемся основанием портала. Вырежем из полосы дюраля отрезок длиной 400 мм. Сразу же отшлифуем его и наклеим сверху шаблон основания портала. Накерним центры отверстий. Нанесем в точки сверления отверстий по капле моторного масла и просверлим все отверстия.
Теперь поместим пластину на фрезерный станок и удлиним отверстия, через которые будет крепиться портал. Нет фрезерного станка - просверлим рядом два отверстия и расточим напильником перемычку между ними. Тщательно отшлифуем пластину и уложим ее на опорные блоки оси X. Слегка прикрутим болтами. Если вы были аккуратны при разметке - болты станут как положено. Если ошиблись - придется слегка рассверлить отверстия в основании портала.
Пока делал забыл какие нужны были размеры Измерим, что получилось Вырезаем боковины портала. Для начала прикинем эскиз портала и оси Z, проверим все размеры: Здесь также как и в первом случае взаимосвязаны боковины и основание оси Z, поэтому тоже расчитываем и рисуем их вместе. Форма боковины определяется не дизайном, а заготовкой, из которой он будет вырезаться. Отпечатав шаблон боковины, накладываем его на полосу дюраля Дюраль берем здесь: Очерчиваем по контуру. Особая точность здесь не важна, только оставьте между двумя частями зазор 3-10 мм. Режем тем, что есть под руками: У меня заготовки вырезаны для дальнейшей обработке на фрезере, если у вас нет такой возможности можете попробовать вырезать болгаркой, ножовкой или лобзиком, постарайтесь сразу сделать все ровно и аккуратно.
Закрепляю одну заготовку на фрезере. Обрабатывать буду нижнюю часть боковины, поэтому выравниваю ее по задней кромке стола. Затем точно так же отрезаю заднюю часть боковины. А для отрезания верхней части боковины, нужно воспользоваться угольником, так как на этот угол будет ложиться уголок - распорка боковин и угол между верхним и задним краями боковины должен быть прямым.
Вот она, боковина: Для изготовления второй сложим эту боковину и заготовку второй и выровняв по переднему краю, стянем струбциной. Теперь можно обрабатывать вторую боковину используя первую, как шаблон. На конечном этапе обработки каждой стороны уберем припуск и с первой, т.е выровняем края сразу у обеих.
Вот что получилось. Теперь сложим обе боковины вместе, тщательно выровняем нижний край, и наложим на боковины шаблон.
Особое внимание на совмещение нижнего края, от этого будет зависеть вертикальность установки фрезера Стянем весь 'пирог' струбцинами у нижнего края и накерним отверстия. Шаблон можно отогнуть или отрезать, он больше не понадобиться Наносим машинное масло на точки сверления Сверлим сначала самое верхнее и самое нижнее отверстия и установив в них болты стягиваем боковины, потом сверлим все остальное. Последовательность сверления: Сквозные отверстия под болты фланцевых креплений, сквозные отверстия под направляющие, сквозное отверстие диаметром не более 20 мм под ходовой винт. Затем в верхней боковине рассверливается на глубину 5-7 мм отверстие диаметром 22 мм под подшипник, пакет переворачивается и на такую же глубину рассверливается такое же отверстие в другой боковине. Отверстия под крепление двигателей делаются только в одной боковине после их разъединения. Теперь наконец возьмем в руки что нибудь измерительное Измерим расстояние от переднего края основания портала до центра каждого длинного отверстия. Разметим нижнюю часть боковины и просверлим отверстия диаметром 5,2 мм Нарежем в них резьбу М6 Прикрутим боковину к основанию портала одним болтом То же самое проделаем и со второй боковиной.
Теперь измерим расстояние между внешними сторонами боковины. Добавим к этому расстоянию удвоенную толщину фланцевого крепления, и отрежем такие направляющие. А заодно подготовим все, для следующего этапа. Берем все это здесь: Измерим расстояние между внутреннними сторонами боковин у основания портала. Вставим верхнюю направляющую и раздвинув верх боковин на такое же расстояние как внизу, вставим направляющую, одев на нее опорные блоки, закрепим верхние фланцы и направляющую в них. Теперь можно вставить и закрепить нижнюю направляющую, предварительно одев на нее опорные блоки.
Вот как должно быть Вырежем пластину основания оси Z и закрепим на ней шаблон Накерним центры отверстий и просверлим отверстия для крепления пластины к опорным блокам и для крепления гайки ходового винта. Теперь можно закрепить пластину на опорных блоках и проверить легкость перемещения основания оси Z по направляющим портала. Чертежи: Принимаемся за изготовление оси Z Основание для нее уже готово, вырежем пластины размером 45х110 для нижней крышки и 60х110 мм для верхней. Для разметки будем использовать только верхнюю крышку.
После разметки центров отверстий сложим верхнюю и нижнюю крышки, выровняв их по боковым краям и особо тщательно - по заднему краю. Просверлим 3 отверстия, через которые крышки крепяться к основанию оси Z и вставив в них болты стянем пластины между собой.
Теперь струбцины можно убрать и продолжить сверление отверстий. Порядок сверления такой: Начинаем сверлить отверстия для направляющих и винта подачи. Когда остается последняя ступенька - 12 мм, вытаскиваем сверло из патрона так, чтобы можно было сразу просверлить сквозное отверстие в обоих крышках: Обильно смазываем отверстия маслом и с одного раза сверлим отверстие под одну направляющую, затем также одним проходом - под другую. Растачиваем отверстие в верхней крышке под подшипник. Отверстие под подшипник в нижней крышке можно рассверлить сразу, перевернув пакет. Я решил изменить способ установки подшипника, закрепляя его не снизу оси Z, а сверху нижней пластины.
Поэтому разъединяю пластины, в верхней крышке сверлю отверстия под крепление двигателя и в торце пластины сверлю отверстия диаметром 4,2 и нарезаю в них резьбу М5 под крепление направляющих: А затем с нижней части этой пластины рассверливаю отверстия под головки винтов крепления двигателя: Рассверливаю отверстие для подшипника в нижней крышке(с верхней стороны) Теперь делаем 'кресло', то есть зажимаем верхнюю крышку и основание оси Z в угловых струбцинах(тисках) Зажимать нужно так, чтобы верхняя крышка накладывалась на верхнюю часть основания оси Z, а задние края были выровнены. Через отверстия в крышке сверлим отверстия диаметром 4,2 мм в торце основания оси Z и нарезаем резьбу М5. Аналогично делаем крепеж под нижнюю крышку. Будьте внимательны, не перепутайте положение верхней и нижней сторон крышек. Скрепляем конструкцию винтами или болтами. Измеряем высоту оси: Отрезаем такой длины направляющие и стачиваем на наждаке с верхней их стороны лыски.

Для удобства сборки снимем фаску не концах направляющих. Вставляем направляющие через отверстия в верхней крышке, нанизываем на них опорные блоки, берем их здесь: обратите внимание как расположены лыски на направляющих и вставив направляющие до конца - зафиксируем их винтами. Теперь проверим соответствие шаблона расположению отверстий в опорных блоках, просто для перестраховки: Вырезаем пластину размером 90х110 мм, накладываем на нее шаблон, сверлим отверстия и прикручиваем к опорным блокам оси Z. Проверяем легкость перемещения и если все нормально - снимаем пластину и через ее нижние отверстия сверлим отверстия диаметром 5,2 мм в кронштейне, а затем нарезаем в кронштейне резьбу и крепим кронштейн к пластине. Я обычно делаю только одно отверстие, центральное и ставлю только на 1 болт, другие два отверстия сверлю после того, как соберу станок полностью и поставлю стол. Так удобнее добиться вертикальности фрезера. Прикручиваем пластину на место: Зафиксируем верхний подшипник.
Делать это можно по разному, я делаю просто, сверлю 2 отверстия, нарезаю в них резьбу и ввинчиваю два самоконтрящихся винта или болта. Ставим ось Z туда где она должна стоять. Проверим соответствие перемещений запланированным. По Z - нормально, после установки стола просвет будет как раз 65 мм, а перемещение оси немного больше - 75 мм. По Y - нормально, лишние 10 мм съедят прессмасленки: А по X казалось бы маловато: Но у нас есть где взять недостающее, достаточно сделать вырез в швеллере спереди: И сзади Конструкция обрела какойто похожий на станок вид: И вес: На этом пока все, продолжение во 2-й части! Филенко ака Trudogolik.
Почти ежедневные отчеты можно читать здесь: Там вся история создания Альтернативы-2 и её модификаций с чертежами в разных форматах. Начиная с 7-й страницы идет описание именно этого станка. А сюда буду выкладывать по мере возможности. Снова снял все размеры, расчитал длину винтов, на осях X и Y буду ставить винты 'внатяг', на оси Z, поскольку там вся нагрузка на нижний подшипник и винт короткий - 'враспор' 'Внатяг' - это который с резьбой, 'враспор' - гладкий. Разделку концов буду заказывать, это единственная работа, которую лучше поручить хорошему специалисту, будь то учитель труда, мастер ПТУ или токарь на заводе. Дальнейшая работа не требовала ни чертежей ни шаблонов, все делалось 'по месту'.
Вырезал из уголка 50х25х3 два отрезка длиной как станок. Это будет защита направляющих Х и боковин от летящей стружки и СОЖ. Уголки закреплены на расстоянии 3-4 мм от боковины портала. Стол будет выфрезеровываться так, чтобы лег на края этих угольников. Тогда стружка гарантированно не попадет на направляющие, а чтобы СОЖ не капала на направляющие - перед сборкой нанесу герметик на край угольников.
Вырезал уступы в краях переднего и заднего швеллеров. Один уступ, чтобы увеличить перемещение по оси X, а маленький для установки боковых щитков. Отрезал два уголка 40х80х4 длиной, равной расстоянию между вертикальными сторонами переднего и заднего швеллеров и закрыл направляющие сбоку и частично снизу. Эти уголки вставлены заподлицо с передним и задним швеллером.
Эти уголки не несут никакой нагрузки, выполняют чисто защитно-декоративнуцю функцию, поэтому привинтил их двумя болтами каждый. Эти же болты будут служить для крепления ножек станка.
И напоследок вырезал и закрепил угольник 120х40х3 мм, который закроет направляющие сзади, укрепит портал в поперечном направлении и сверху на него можно уложить кабель-канал. К концу работы станок обрел такой вид: Пока все. Продолжаю, назло буржуазным стриптизерам. Пока винты в работе, займусь столом. Буду делатиь его из дюраля Д16 толщиной 12 мм. Измеряю расстояние между стружкозащитными угольниками и длину стола.
Из ровного листа дюраля вырезаю прямоугольник, длиной по длине станка, а шириной на 15 мм шире расстояния между стружкозащитными угольниками. Вдоль длинных сторон с нижней стороны листа профрезеровываю выступ шириной 10 и высотой 4 мм. Это нужно для того, чтобы можно было герметизировать стык между столом и стружкозащитным угольником, тогда можно будет использовать СОЖ. На ненужный лист ДСП или мебельный щит накладываю лицевой стороной вниз лист фанеры, толшиной 6-8 мм и размером в размер стола. Можно вместо фанеры использовать пластик толщиной 2-5 мм На этот лист накладываю нижней стороной вверх заготовку стола и делаю разметку отверстий.
Разметку можно выполнить как угодно, я обычно отступаю 20 мм обоих от боков стола, сверлю ряд отверстий с шагом 50 мм. Затем отступив еше 50 мм еще ряд и так далее. По центру стола оставляю полосу шириной более 50 мм, чтобы стружка со стола через отверстия не попадала на ходовой винт.
После разметки сверлю отверстия диаметром 5,2 мм в столе и сразу же в листе фанеры. Сначала делаю угловые отверстия и вставляю в них болты, чтоб заготовка стола и фанера не 'расползлись', затем сверлю все отверстия. Снимаю дюралевый стол с фанеры и с лицевой его стороны зенкую отверстия. Затем вооружаюсь шуруповертом, с зажатым в патроне метчиком М6 и периодически окуная метчик в моторное масло нарезаю резьбу во всех 60-ти отверстиях. Отверстия с передней и задней сторон стола рассверливаю сверлом М10 на глубину 5 мм.
Уложив стол на станок, выравниваю передний край и в переднем и заднем швеллерах делаю отверстия диаметром 6 мм для крепления стола. Снимаю стол и шлифую его шлифмашинкой. НА последнем этапе шлифовки насыпаю на стол немного порошка 'Пемоксоль' и добавив воды, дошлифовываю с порошком. Порошок снимет последний тонкий слой, а моющие вещества, содержащиеся в нем отмоют дюраль от масла и грязи. Осталось сполоснуть стол водой и дать просохнуть: Стол белый, как зубы Кикабидзе!
Теперь сделаем прижимы для деталей. Долго мудрить не буду, возьму струбцину от FIT, обрежу лишнее, просверлю отверстие диаметром 6 мм и накрутив гайку на болт, можно зажимать детали на столе. Теперь вернемся к оставшейся фанерке. Вспомним что нижняя ее сторона лицевая, рассверлим отверстия до диаметра 8 мм. Отшлифовав обе стороны фанерки, получим жертвенный стол, который при износе можно использовать как шаблон для новой 'жертвы', так как отверстия в нем строго совпадают с отверстиями стола. Ну на сегодня все!
Valb, в хоббийном станкостроении АБСОЛЮТНО все конструкторы станков, и Граф и AlexSpb и Vasilij и несколько десятков других, маститых и начинающих, делают все своими руками или собирают своими руками из того, что заказали на заводах по своим чертежам. К тому же среди станкостроителей нет ни одного, кто прятал бы свои станки от народа, плохи они или хороши. И нет ни одного, кто мог бы неаргументированно охаять чужую конструкцию, как и из чего бы она ни была сделана. Посмотрите конструкции Tima, по мнению таких как dpm они вообще не должны работать и рассыпяться в пух и прах при первом включении. И делают шедевры.
Вот этот орнамент сделан на станке размером 2000х1000х100. А сам станок сделан из древесно стружечных плит и листового металла. Болгаркой, дрелью и предыдущим станком. Здесь история создания станка Tima: Для станка нам понадобится корпус для электронной начинки и блока питания. Его можно купить, а можно простыми способами изготовить из крышки старого системного блока. О том как это сделать читайте здесь: Внимание!
От Сертификат соответствия (на сэндвич панели с минеральной ватой) срок действия до Экспертное заключение (на сэндвич панели с минеральной ватой) Пожарный сертификат (на стеновые сэндвич панели с минеральной ватой) срок действия до Пожарный сертификат (на кровельные сэндвич панели с минеральной ватой) срок действия до Сертификат соответствия (на сэндвич панели с пенополистиролом) срок действия до Экспертное заключение о соответствии санитарным нормам. 06.201 8 Гигиенический сертификат (пенополистирол) от 02.07.20 15 Результаты специальных испытаний пенополистирола на наличие фосгена. (на сэндвич панели с пенополистиролом) от Пожарный сертификат (на стеновые сэндвич панели с пенополистиролом) срок действия до 02.1 0.201 9 Пожарный сертификат (на кровельные сэндвич панели с пенополистиролом) срок действия до 23.1 1.201 8 Сертификат соответствия (профнастил С 10, С 21, НС35) срок действия до Сертификат соответствия (профнастил НС60, НС75) срок действия до 03. Сколько стоят пластиковые панели.
Объем файла около 7 мегабайт!!!! В этот корпус входит плата распростаненного контроллера на микросхемах L297+L298 и трансформатор питания из принтера Star, а также все остальное, что нужно для станка. Устройство и работу еще одного настольного станка, изготовленного мной можно посмотреть здесь: А здесь работа примитивной модели плазмореза: Позже добавлено автором: Гайки. Конструкция разработана под гайки на основе опорных блоков SC12UU, но не требует изменений и для установки таких гаек от CNCMASTERKIT или гаек DFU1-10x2 DFU1-12x3, предлагаемых фирмой Purelogic. Расстояние от центра винта до опорной плоскости у всех гаек равно 15 мм. Крепяться эти гайки по месту. Здесь я буду устанавливать гайки с компенсацией винта, да еще и с регулируемым преднатягом.

Делаю их просто. Основа - корпус от опорного блока SC12UU из которого удален линейный подшипник LM12UU, который может использоваться как запчасть для оси Z.
Из капролона, делрина или бронзы вытачиваются 4 круглые гайки, 2 из них должны входить в корпус SC12UU очень плотно,это будут базовые гайки, а две с небольшим скольжением, это гайки регулировки люфта. Базовые гайки вставляются в корпуса и закрепляются винтами, для которых сверляться отверстия диаметром 3,3 мм и нарезается резьба М4. Для гаек регулировки тоже сверлится отверстие и нарезается резьба М4. ГАйка накручивается на винт Теперь гайка регулировки накручивается по винту до тех пор пока не войдет в корпус и не упрется в него. Вращая винт проверяем преднатяг, а вращая гайку - регулируем его. Добившись желаемого, фиксируем гайку регулировки винтом. В станке гайки установлены так, что доступ к гайке оси Х осуществляется снизу стола, а для доступа к регулировке гайки портала необходимо снять угольник-распорку.
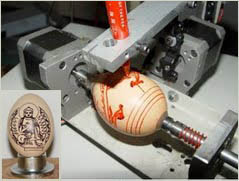
Гайка оси Z несколько другая, она имеет размер 40х20х30 мм и изготовлена из графитонаполненного капролона, можно также применять бронзу, делрин, обычный капролон. В будущих конструкциях эта гайка будет заменена на гайки размером 30х40х40 мм. Установку гаек будем делать одновременно с установкой винтов. Винты в станок можно поставить любые.
Например, даже М8, строительные шпильки стоят очень дешево, поэтому кто спешит, может потренироваться на шпильках. У меня будут использоваться трапецеидальные винты ТР12х3 во всех осях. Эту операцию можно начинать делать сразу после изготовления оси X, поэтапно. Но я делаю когда все детали станка готовы и когда можно проверить почти все необходимые расстояния. Выверяем расстояния от направляющих оси X до опорной плоскости стола. Для этого снимем портал, стружко-защитные угольники и боковые крышки. Основание портала должно свободно перемещаться по своим направляющим.
Станок Графа Чертежи
Проверяем затяжку болтов. Которыми крепится основание к опорным блокам и переворачиваем ось X ввсерх тормашками. Затягиваем винты крепления направляющих и расслабляем болты крепления хомутов. Под своим весом направляющие переместяться вниз.
Теперь слегка затянем болты крепления хомутов и перевернем ось X. Измеряем расстояние от верхней полки швеллера до основания портала во всех 4-х углах оси Х. Если все сделано по первому чертежу и толщина основания равна 10 мм, то от полки швеллера до основания портала должно быть немного меньше 13 мм. Постукивая через деревянную проставку по краю направляющей, выставим в каждом углу строго 13 мм. Если есть более точный инструмент чем штангенциркуль, например индикатор часового типа, выставим одинаковое расстояние от полки швеллера до верхней точки направляющих во всех 4-х углах.
Станок Графа Чертежи Скачать
Затянем болты крепления хомутов и еще раз проверим. Во время этой операции необходимо передвигать основание портала в ту сторону, где проводиться проверка и не допускать, чтобы основание перемещалось туго. Теперь закрепим ходовую гайку и ввинтим в нее через отверстие в швеллере ходовой винт.
Станок Графа Чертежи
Винт должен точно попасть в отверстие в противоположном швеллере. Повращайте винт, если выясниться, что он кривой, повторите операцию после правки винта. Если конец винта смещен, сместите гайку, подложите под нее лист тонкой фольги или наоборот сошлифуйте часть гайки. Если все расстояния одинаковы, и винт расположен точно по отверстиям, можно заштифтовать фланцевые крепления направляющих. Для этого через швеллер сверлится отверстие в фланцевом креплении и в него туго забивается штифт, например цилиндрическая часть обломка сверла. Выступающая часть штифта зашлифовывается. Теперь можно проверить горизонтальность направляющих портала.
Портал ставится на место и прикручивается 4-мя болтами. Используя штангенциркуль и передвигая ось Z вправо и влево, измеряем расстояние от оси Z до верхней полки переднего швеллера. Штангенциркуль располагается в отверстии для крепления фрезера. Более точно можно проверить расстояние индикатором часового типа, причем нам важно не само расстояние, а чтобы это расстояние справа и слева было одинаково. Если расстояния не одинаковы, можно сточить низ более высокой боковины, но стачивать нужно по всей нижней части одинаковый слой, чтобы не нарушить перпендикулярность направляющих оси Y.
Можно под более низкую боковину подложить полоску фольги. Добившись одниаковой высоты, укладываем и прикручиваем на место стол. Теперь проверяем расстояние от оси Z уже в нескольких точках по всей поверхности стола. Если предыдущие операции были выполнены тщательно, то разница в расстояниях может быть только из-за неровности стола, попробуйте его прошлифовать. Какая должна быть разница, каждый определяет для себя самостоятельно, чем она меньше, тем легче и удобнее будет работать на станке. Из юстировочных операций нам осталась только одна - проверка и регулировка перпендикулярности направляющих осей X и Y, но эту операцию мы сделаем уже после запуска станка. Также после запуска добъемся вертикальности фрезы.